Ensuring reliable sterilization is non-negotiable in medical device manufacturing and hospital practices. Among the various sterilization technologies available, the ETO Sterilizer Machine offers unmatched versatility. It is especially suitable for devices sensitive to heat and moisture, making it a staple in healthcare sterilization departments and medical equipment factories.
What truly defines the performance and trustworthiness of these industrial sterilizers is the synergy between their stainless steel chamber, aeration capabilities and their ability to detect leaks before the sterilization cycle begins. Let’s explore these core components in depth.
Stainless Steel Chambers in ETO Sterilizer Machines: Structure Meets Safety
At the heart of every ethylene oxide chamber is its structural material. High-grade stainless steel – commonly SS304 or SS316 – is used to construct both the chamber interior and the sterilizer door. This material ensures durability, corrosion resistance and chemical stability, even under repeated exposure to ethylene oxide.
The chamber must withstand extreme variations in pressure during the vacuum and sterilization phases. Whether it’s a single door or double door configuration, the design ensures operational reliability, cleanroom compatibility and compliance with medical sterilization protocols.
The chamber’s internal design also promotes efficient gas dispersion. Integrated fans and strategically placed gas nozzles allow EO gas sterilizer to reach every instrument in the load uniformly, maximizing sterilization effectiveness and reducing cycle variability.
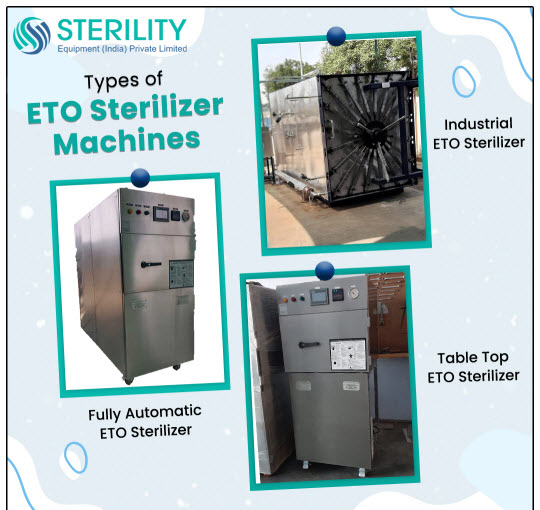
Sterilization Cycle Phases and Chamber Monitoring in EO Sterilizers
Modern sterilizer machines operate through highly controlled phases: pre-conditioning, vacuum draw, EO gas injection, exposure and aeration. These cycles rely on the chamber’s ability to sustain both negative and positive pressures.
Digital control systems monitor real-time parameters – temperature, pressure, relative humidity (RH) and exposure time. This data is not only displayed on intuitive control panels but also logged for compliance, quality checks and audit trails. Reports and graphs can be exported via USB drives, aligning with FDA and ISO documentation requirements.
Aeration Systems in ETO Sterilizer Machines: Minimizing EO Gas Risks
One of the most critical aspects of medical device sterilization with EO gas is the post-process aeration phase. Integrated aeration systems are designed to mitigate this threat by accelerating gas removal from sterilized materials.
These systems operate under tightly controlled conditions, optimizing airflow, temperature and humidity. A dedicated RH control system – often supported by steam generators – ensures that the aeration environment does not compromise the structural integrity of the sterilized devices.
Aeration is seamlessly integrated into the sterilization cycle. Once the exposure phase is completed, the sterilizer transitions into aeration mode without manual intervention, reducing operator risk and enhancing workplace safety.
EO Sterilizer Machine Control Systems: Accuracy in Every Cycle
Precision is fundamental in EO sterilization. The embedded control system regulates every critical variable – vacuum strength, chamber temperature, humidity and gas concentration. By doing so, it guarantees repeatable outcomes across sterilization cycles.
Automated alerts notify operators of system inconsistencies and interlocks prevent cycle initiation until all safety and sterilization parameters are met. The intuitive user interface displays each cycle stage – vacuum, eo sterilisation exposure, aeration – making it easier for operators to monitor processes and troubleshoot issues.
Leak Test Function: Safeguarding EO Sterilizer Machine Performance
A non-negotiable step before each cycle in an ethylene oxide sterilizer is the leak test function. This function ensures that the chamber maintains vacuum integrity and that no EO gas will escape during the sterilization process.
The leak test is typically conducted by drawing a vacuum and measuring any pressure increase over time. A consistent pressure reading confirms chamber integrity, while any anomaly prompts the system to halt the cycle and alert the operator. This not only ensures operator safety but also prevents ETO sterilization waste and under-sterilized devices.
This step also supports long-term equipment health by identifying seal or valve issues early, preventing mechanical failures and ensuring uninterrupted performance in high-demand environments.
Sterilization Chamber Pressure Control: Positive and Negative Dynamics
The ability to switch between positive and negative pressure environments within the sterilization chamber is vital. Negative pressure is essential during vacuum stages to remove air and improve EO penetration, while positive pressure is used during aeration to safely vent residual gas.
This dynamic pressure management contributes to effective sterilization of complex instruments and porous materials, ensuring that even the hardest-to-reach areas are free from microbial contamination.
How EO Sterilization Supports Diverse Medical Devices?
EO sterilization is a preferred method for treating complex or sensitive items such as catheters, surgical kits and plastic-based devices. These devices may degrade under steam or radiation, but EO gas can sterilize without heat, preserving the material integrity.
The combined action of stainless steel chambers, controlled aeration and validated leak detection, these machines are able to meet the most demanding sterilization challenges without compromising patient safety or device functionality.
Conclusion
The design and performance of ETO Sterilizer Machines are rooted in precision engineering. By focusing on three key elements – stainless steel chamber construction, automated aeration systems and leak detection protocols – these industrial sterilizers ensure complete and safe medical sterilization every time.
The success of ETO sterilizer lies not only in the potency of ethylene oxide gas but also in the machine’s ability to manage, monitor and document each cycle with surgical accuracy. With growing demand for sterility in modern healthcare, machines that offer this level of performance and safety will remain indispensable.